Gasification Systems
The U.S. Department of Energy (DOE) Gasification Systems Program is developing innovative technologies and designs for converting diverse types of solid feedstocks into synthesis gas to enable the low-cost production of hydrogen, transportation fuels, chemicals, electricity and other useful products to suit market needs. Advancements in this area will help enable syngas-based technologies and energy systems to be competitive in both domestic and international markets, and spur on the use of abundant domestic resources towards increased energy dominance and energy security of the United States.

Supporting Essential Initiatives and Goals
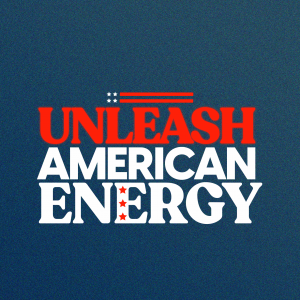
Use of Domestic Energy Resources
Gasification is a versatile technology able to convert solid fuels such as coal into synthesis gas (syngas). Syngas has extreme process versatility, suitable for electrical power generation or conversion into high-value products such as hydrogen, liquid fuels and chemicals such as ammonia and fertilizer. Polygeneration plants that produce multiple products are uniquely possible with gasification technologies. Carbon dioxide can be efficiently captured from syngas, enabling its utilization (such as for enhanced gas recovery/enhanced oil recovery) or safe storage. Gasification can play a unique role in leveraging America’s vast reserves of solid fossil fuel resources for multiple, versatile energy systems and value-added production.
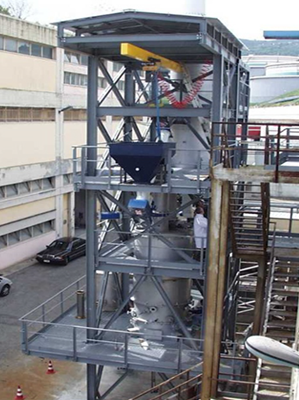
Energy Innovation
Gasification research and development is an important component of overall technology development efforts that DOE is pursuing to advance affordable, reliable and secure energy technologies, including those for fossil fuels, and strengthening American energy dominance.
Gasification Versatility & Synergies
Gasification processes have inherent flexibility for accepting many types of solid feedstocks such as coal and solid wastes and converting those into a range of high-value products such as liquid fuels and chemicals such as ammonia, hydrogen, electric power, and more. Byproducts from coal gasification include ash/slag and sulfur, which have uses in building aggregate/cement and sulfuric acid manufacture, respectively. Coal contains minerals including rare earth oxides/elements, which are enriched in the solid byproducts of gasification (ash); on this basis, coal gasification has a synergy with critical minerals/materials specifically rare earth element recovery.
Explore Key Technology Areas
The research and development efforts of the Gasification Systems Program apply primarily to three key technology areas, advances in which will best contribute toward increased efficiency, enabling cost reductions, and supporting increased market deployment of gasification/syngas-based energy systems. These three technology areas are: (1) Process Intensification for Syngas & Hydrogen, (2) Air Separation Technology, and (3) Novel Technologies for Chemicals and Fuels.
Process Intensification for Syngas & Hydrogen
Research addresses control of chemical reactions in increasingly modular and intrinsically efficient reactors, allowing for smaller reactors and streamlined process systems for gasification, syngas cleanup and syngas conversion.
Air Separation Technology
Research focuses on identification of new concepts and technologies for production of oxygen for use in gasification systems.
Novel Technologies for Chemicals & Fuels
Research concerns designs and strategies for gasification-based technologies/systems using fossil fuels and opportunity feedstocks for production of chemicals, liquid fuels and hydrogen, all valuable products for the U.S. economy.
Gasification Compendium
A summary of research and development projects and activities sponsored by DOE/NETL’s Gasification Systems Program.
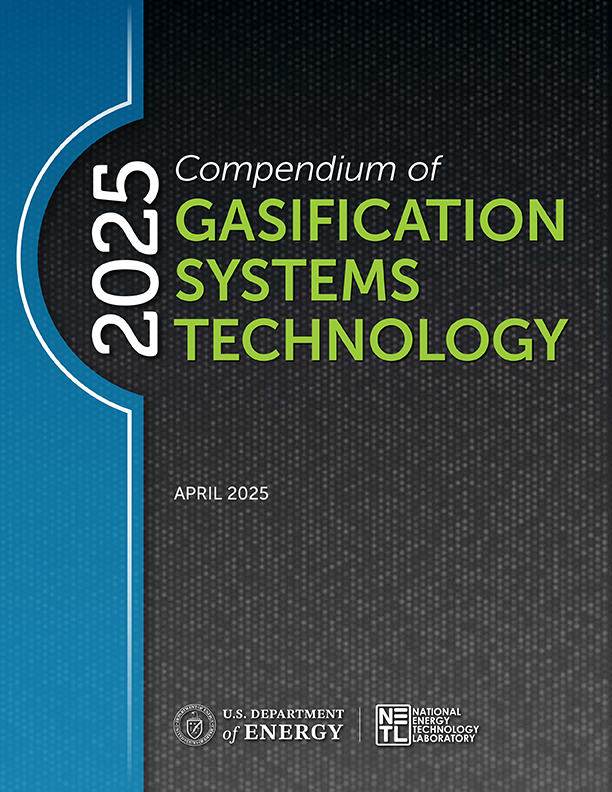
Explore the Site
The Gasification Systems Program pursues technology advancements in these areas through on-site work at NETL, and by external funding opportunities resulting in a suite of projects performed by industry, academia, and other national laboratories, and overseen by NETL.
Your Comments: We hope the information provided in these webpages proves of value. We welcome any comments, suggestions, or questions you might have &emdash; Click the contact button at the top of the page with Comments, Suggestions or Questions.
NETL implements this effort as part of DOE’s Advanced Energy Systems Program.