Point Source Carbon Capture
Advancing technologies for the capture of CO2 from point sources, such as natural gas power and industrial facilities, with minimum cost and energy penalty
The U.S. Department of Energy/National Energy Technology Laboratory’s (DOE/NETL) Point Source Carbon Capture Program is developing the next generation of advanced carbon dioxide (CO2) capture concepts to support the United States in achieving ambitious goals for a greenhouse gas (GHG)-neutral economy by 2050, a carbon-pollution-free power sector by 2035, and a 50% reduction from 2005 levels in economy-wide net GHG pollution by 2030. DOE’s Office of Fossil Energy and Carbon Management (FECM) has adopted a comprehensive, multi-pronged approach for carbon management that involves the coupling of carbon capture methods (i.e., point source carbon capture for fossil fuel-based power generation and industrial sources; and carbon dioxide removal (CDR) technologies co-located with low-carbon energy sources) with long-duration carbon storage or CO2 utilization/conversion into long-lasting products. The Point Source Carbon Capture Program is accelerating commercially deployable solutions that can be applied to a wide spectrum of CO2 emissions sources, including facilities that produce power, hydrogen, ethanol, cement, or steel. Projects range from conceptual engineering and materials design at laboratory and bench scale (Technology Readiness Level [TRL] 2-5) to large-scale testing and front-end engineering and design (FEED) studies (TRL 6-7) to lower both capital and operating costs and improve the economics of point source carbon capture.
The Point Source Carbon Capture Program is advancing technologies to minimize the environmental impacts of fossil fuel-based power generation and to decarbonize existing infrastructure in the power and industrial sectors. Research and development (R&D) efforts to date have led to reductions in both capital and operating costs through implementation of energy and process efficiencies and development of advanced CO2 capture media (e.g., solvents, sorbents, and membranes). To achieve deep decarbonization of emissions sources, the program is focused on developing highly efficient, scalable carbon capture technologies with even further cost reductions, that are capable of operation under a flexible duty cycle, and that can achieve greater than 95% carbon capture.
Point Source Carbon Capture
Capture from Power Generation Sources
Point source CO2 capture in fossil fuel-based power production separates CO2 emissions from the plant’s exhaust gas or syngas stream. The Point Source Carbon Capture Program is focused on advancing novel carbon capture materials, equipment, processes, or a combination thereof for applications in natural gas combined cycle (NGCC) power generation. R&D is underway to support testing of highly efficient component designs, material systems, and/or integrated processes and to conduct FEED studies for commercial-scale CO2 capture at existing NGCC power plants.
Capture from Industrial Sources
Point source CO2 capture from industrial facilities, such as mineral production (cement and lime) plants, iron and steel manufacturing plants, hydrogen production plants, and ethanol plants—in which CO2 emissions may be present at a higher concentration than fossil fuel-fired power plants—is a vital element in reducing CO2 emissions. R&D is underway to test transformational capture technologies for industrial carbon capture and to conduct initial engineering design and FEED studies on commercial-scale capture systems that separate CO2 emissions at industrial facilities.
Point sources of CO2 such as power plants can result in output of byproduct residuals that can either be gainfully recycled or end up as a disposal liability. Also, various non-CO2 emissions may be impacted as CO2 capture retrofits are applied. R&D is underway to develop technological improvements and solutions for management, disposition, and remediation of these residuals and non-CO2 emissions. Possibilities to increase beneficial use of residuals, to safely manage and disposition aging inactive/legacy residuals impoundments, and to use innovative technologies such as plant-based stabilization and monitoring in environmentally sound approaches, are in scope of investigation. These efforts will promote environmental justice and help advance decarbonization efforts over the coming decades.
Key Analysis Areas
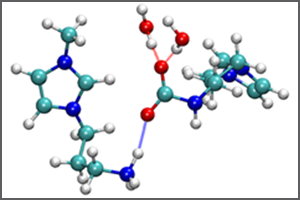
Solvents
Solvent-based CO2 capture involves chemical or physical absorption of CO2 from a gas into a liquid carrier. R&D of advanced solvents (e.g., water-lean solvents, phase-change solvents, high-performance functionalized solvents) that have a lower regeneration energy requirement than existing amine systems, combined with high CO2 absorption capacity and tolerance to impurities, is a key objective for lowering capture costs. System advancements include process intensification techniques, methods to mitigate aerosol formation and corrosion, and heat integration approaches.
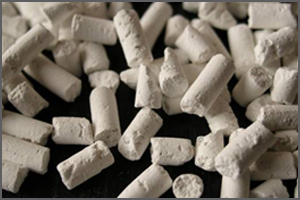
Sorbents
Sorbent-based CO2 capture involves the chemical or physical adsorption of CO2 from a gas using a solid sorbent. R&D objectives include low-cost durable sorbents that have high selectivity for CO2, high CO2 adsorption capacity, resistance to oxidation, and can withstand multiple regeneration cycles with minimal attrition. System advancements include sorbent process intensification techniques, novel reactor designs, and enhanced process configurations, such as rotating beds for CO2 adsorption and desorption.
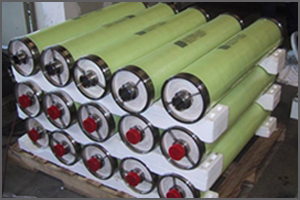
Membranes
Membrane-based CO2 capture uses permeable or semi-permeable materials that allow for the selective transport and separation of CO2 from a gas. Membrane processes offer potential advantages when compared to other CO2 separation technologies, including no hazardous chemical storage, handling, disposal, or emissions issues; simple passive operation; tolerance to high sulfur oxide [SOX] and nitrogen oxide [NOX] content; a reduced plant footprint; and efficient partial CO2 capture. R&D objectives include development of low-cost, durable membranes (e.g., polymeric membranes, mixed matrix membranes, sub-ambient temperature membranes) that have improved permeability and selectivity for CO2, thermal and physical stability, and tolerance to gas contaminants. Process enhancements for membrane-based capture systems include low-pressure drop membrane modules.
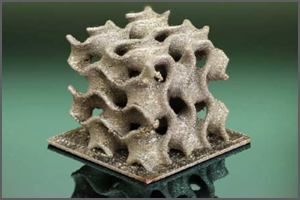
Novel Concepts
Novel concepts include alternative technologies and processes, such as cryogenic separation and electrochemical membranes, and additive manufacturing of novel system components and materials. R&D objectives include development of equipment, materials, and processes that enable intensified thermodynamic operations, improve process performance, and reduce equipment size, lowering capital and operating costs.
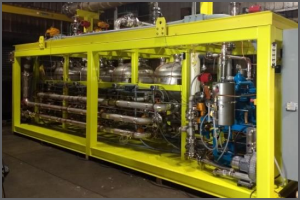
Hybrid
Hybrid systems efficiently combine two key technologies in a single system (e.g., sorbent-membrane system). Hybrid concepts can reduce the overall energy intake of the process by leveraging process synergies, resulting in a more cost-effective system.
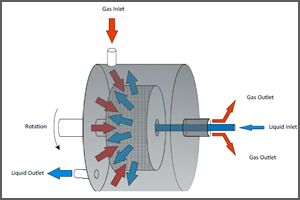
Enabling Technologies
Enabling technologies are concepts that could improve a whole class of materials, and although the research might be applied to one specific material, it is envisioned that substantial research findings could benefit multiple materials. R&D topics include solvent aerosol emissions mitigation, solvent viscosity reduction, solvent stability improvements, materials compatibility, corrosion resistance improvements, and degradation products reduction or separation.