Computational Science and Engineering
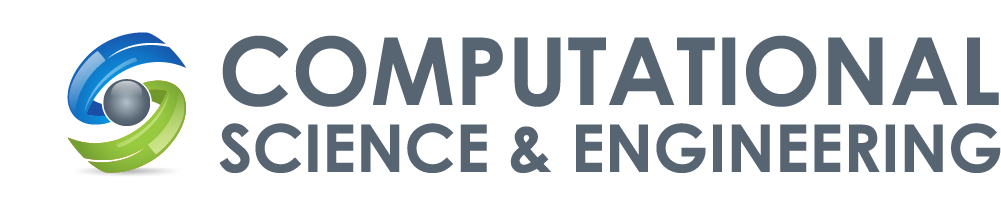
NETL’s Computational Science & Engineering (CSE) Directorate develops science-based simulation models, mathematical methods and algorithms, and software tools required to address the technical barriers to the development of next-generation technologies. CSE works together with other directorates at NETL to generate information and understanding beyond the reach of experiments alone. Through the integration of experimental information and computational sciences, scientists and engineers can simulate variations more efficiently while saving time, money, and materials.
The CSE Directorate is organized into three research teams that collectively maintain NETL’s Computational Science and Engineering competency:
- The Computational Materials Engineering Team model’s materials at the atomic, molecular and microstructural scales, which enables a fundamental understanding of materials behavior and provides insight into subsequent materials development opportunities and optimization strategies
- The Computational Device Engineering Team develops multiphase computational fluid dynamics models required for predicting the performance of fossil energy devices, such as advanced combustion reactors, gasifiers, emissions capture, and carbon dioxide (CO2) capture units. The team has robust capabilities for linking models at multiple scales to increase simulation fidelity.
- The Science-Based Artificial Intelligence/Machine Learning Institute (SAMI) is developing and using data science methods to gain scientific insight from complex, high-dimensional, high-volume data sets from experiments and simulations conducted in support of energy technology development and is beginning to use machine learning to advance energy technology development. Learn more about Artificial Intelligence, Machine Learning, and Data Analytics:
Together, the CSE Directorate teams leverage world-class expertise and facilities to enable NETL’s simulation-based engineering approach for accelerating the development and deployment of novel fossil energy materials, processes and device designs.
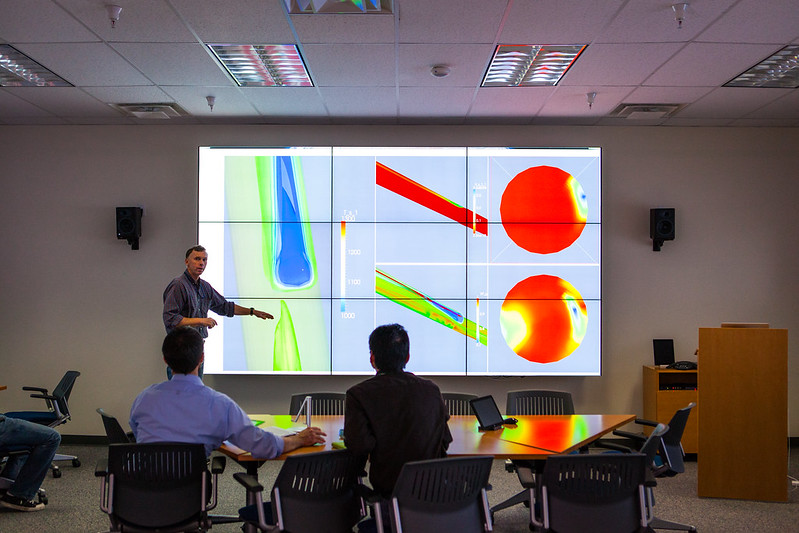
Explore the Site
This research supports NETL’s Computational Science & Engineering competency.