Existing Plants Combustion Technologies
Technology Options to Improve the Efficiency, Longevity, and Competitiveness of the Existing Coal Fleet
The existing coal power generating fleet plays a critical role providing reliable power generation required for power grid stability. It is important that these existing units continue to operate in an efficient and reliable manner. Under the current energy landscape, power plants are often required to operate at low and/or variable loads. Since the plants are not designed to operate below baseload, operation at low-load results in lowered efficiency and increased wear on the plant components. Operation at variable loads requires ramping of the plant capacity, which adds to the lowered efficiency and increased wear on plant components. As a result, there is a need for rapid commercialization of technologies to improve the efficiency, reliability, and flexibility of existing coal-based power plants. Existing plant combustion technologies research and development (R&D) focuses on the identification of impactful, near-term opportunities applicable to the needs of the existing fleet.
R&D has been initiated on cost-effective technologies expected to bring about near-term (three to five years) benefits for incorporation into commercial plants that will continue to operate on coal into the future. Currently, the National Energy Technology Laboratory (NETL) supports several Existing Plant Combustion Technologies projects in collaboration with academia, industry, and NETL’s Research and Innovation Center (RIC), ranging from bench-scale testing to validation testing in actual coal-fired power plants.
Reliability Improvements
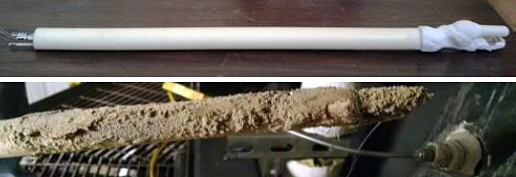
To alleviate reliability impacts, the Transformative Power Generation Program is investigating technologies that could improve reliability and availability, as well as reduce maintenance costs. Innovative technologies being researched include online sensors, instrumentation, algorithms, and failure mode detection systems to monitor key plant components and inform possible repairs. One such concept is condition-based monitoring, a maintenance philosophy that actively monitors the condition of equipment to predict failures and schedule maintenance to maximize availability and generating capacity while saving cost. R&D is also being performed on tools for predicting the life of critical equipment to ensure long-term safety and reliability of existing plants.
Operational Flexibility
For a significant fraction of the existing coal-fired fleet, flexible operation (i.e., low-load operation and frequent deep cycling) has become the normal operating condition. Technology development efforts are focusing on rapid cycling and methods for responding to load changes. Advanced control methods for monitoring coal pulverizer operation and controlling steam and gas temperatures at low loads are being studied to improve the performance and economics of existing power plants. The implementation of neural networks and sensor technologies enables intelligent control for optimal combustion system performance and can improve flexible operation capability.
Efficiency Improvements
Improving plant efficiency is critical to the economic viability of a coal-fired power plant. Technology solutions are being investigated to improve efficiency of existing plants during both transient and steady-state operation, leading to reductions in operating cost and emissions. The Transformative Power Generation Program is identifying plant upgrades and areas for potential R&D to improve boiler and steam cycle efficiency, as well as to reduce auxiliary power. Improvements to the steam cycle efficiency involve additional steam generation, pump and cooling tower upgrades, and advanced ultra-supercritical (A-USC) retrofit options that include increased steam temperature and use of advanced materials for enhanced heat transfer efficiency. Efficiently recycling resources such as waste heat and water also presents advantages for increasing plant efficiency and reducing costs.