1. Demonstrate Ultra-low NOx Combustion in the Scale-up Prototype
Under high-heat recirculation, the combustion reaction in the Swiss-roll can be sustained at lower (premixed) combustion temperatures (1000~1200ºC), resulting in extremely low NOx formation (< 1 ppm). ACT hosted Zeeco on June 22, 2016, to demonstrate this ultra-low combustion feature in the scale-up Swiss-roll prototype. The demonstration went well and Zeeco expressed interest in exploring the use of the Swiss-roll as an advanced incineration device. Table 1 shows multiple measurements of different species concentrations in the exhaust.
Table 1. The NOx and other species measured from the exhaust of the scaled-up Swiss-roll. |
Log No.
|
Fuel
|
O2
|
CO2
|
CO
|
NO
|
NO2
|
NOx
|
SO2
|
Units
|
57
|
Propane
|
19.5
|
0.9
|
781
|
0
|
0
|
0
|
-
|
ppm
|
58
|
Propane
|
19.6
|
0.9
|
710
|
0
|
0
|
0
|
-
|
ppm
|
59
|
Propane
|
15
|
3.9
|
37
|
1
|
0
|
1
|
-
|
ppm
|
60
|
Propane
|
16.7
|
2.8
|
34
|
1
|
0
|
1
|
-
|
ppm
|
61
|
Propane
|
16.7
|
2.8
|
35
|
0
|
0
|
1
|
-
|
ppm
|
62
|
Propane
|
16.6
|
2.8
|
36
|
1
|
0
|
1
|
-
|
ppm
|
63
|
Propane
|
16.6
|
2.8
|
36
|
1
|
0
|
1
|
-
|
ppm
|
64
|
Propane
|
17.2
|
2.4
|
43
|
1
|
0
|
1
|
-
|
ppm
|
65
|
Propane
|
17.4
|
2.3
|
56
|
1
|
0
|
1
|
-
|
ppm
|
66
|
Propane
|
17.4
|
2.3
|
68
|
1
|
0
|
1
|
-
|
ppm
|
|
2. Demonstrate the Stable Incineration with Low Heating Value Biogas
Zeeco suggested that the initial potential application is for landfill biogas incineration. In the later life of the landfill, the heating value of the biogas is too low to have stable incineration by itself, and a significant amount of supplemental fuel is needed to sustain the combustion process. Since the Swiss-roll is able to have stable combustion with very low heating value feedstock, it can potentially be used in this application to reduce the cost of supplemental fuel. A simulated biogas (55% CH4 and 45% CO2) test was performed to demonstrate the low heating value combustion in the Swiss-roll incinerator.
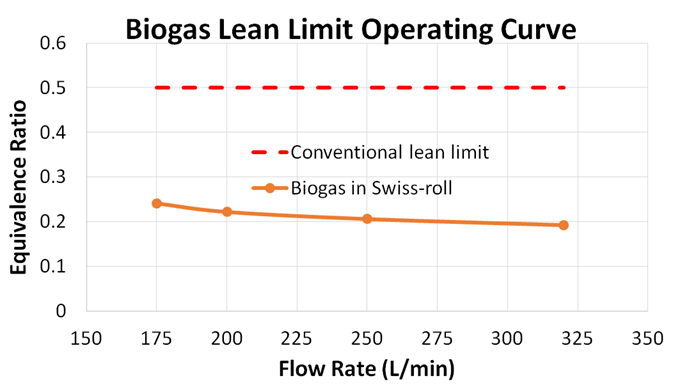 |
Figure 1. The lean limit of the low heating value biogas (indicated via equivalence ratio) tested in scale-up Swiss-roll. (click to enlarge) |
3. Design and Build a Swiss-roll with Modified Center Reaction Zone
While the low heating value combustion has been demonstrated, one challenge of using the Swiss-roll for the landfill application is the requirement of high process flow rate. At the later life of the landfill, it still has ~500 CFM of biogas flow rate, plus the large amount of air needed. This high flow rate results in anextremely large Swiss-roll size requirement. In addition, the current reaction zone, which is constructed by two half circle sheet metals, tends to deform due to high center reaction temperature (Figure 2 Left). To address these challenges, a new center reaction zone design was developed. The new reaction zone is a solid cylinder with the flow introduced from one end and leaving from the other end. As with the typical Swiss-roll design, this center reaction is surrounded by the spiral heat exchanger to recover the heat (Figure 2 Right). The new design is expected to have better structural integrity and also accommodate high flow rate due to reduced center flow speed. The new Swiss-roll is currently under construction and will be completed and tested soon.
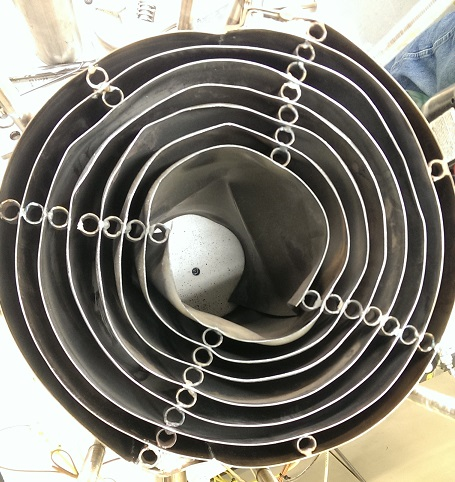 |
Figure 2. Left: The center of the previous scale-up Swiss-roll deformed due to high reaction temperature. Right: The new design Swiss-roll with modified center reaction zone (a solid cylinder with thicker wall) to accommodate higher flow rate and higher center reaction temperature.
|
4. Heating Applications
In addition to the potential landfill application, the ultra-low NOx combustion feature may be applied to other combustion-related devices. ACT recently had a teleconference with engineers from Trane, who is a leading manufacturer of heating and cooling systems. They expressed the interest on using Swiss-roll for the combustion device for residential and commercial heating applications. The motivation is due to the recent environmental regulation in California (rule 1111) that requires the NOx emission of those devices be reduced from 40 ng/J to 14 ng/J. While the Swiss-roll has been demonstrated to be able to achieve very low NOx combustion, it has not been demonstrated for heating application. To explore the possibility of using the Swiss-roll for this application, a method to extract heat from the Swiss-roll is currently being designed (Figure 3).
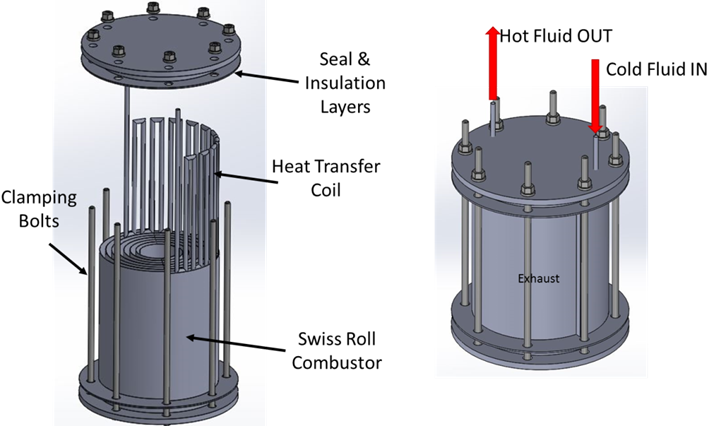
Figure 3. Schematic of method to extract heat from Swiss-roll. |