History
Over the past century, NETL and its predecessor facilities have spearheaded advancements in energy research and technology. The Lab continues to be dedicated to advancing the nation’s energy future by creating innovative solutions that strengthen the security, affordability and reliability of energy systems and natural resources.
1910
Congress passes the Organic Act, authorizing the creation of the U.S. Bureau of Mines within the U.S. Department of the Interior (DOI). The Bureau aims to increase health, safety, economy, and efficiency in the mining, quarrying, metallurgical, and miscellaneous mineral industries of the country.
1918
In response to new oil discoveries in Oklahoma and Texas, the Petroleum Experiment Station is established in Bartlesville, Oklahoma. This becomes one of 17 DOI Bureau of Mines facilities under Public Law 283 (63rd Congress, 1915). The Station applies engineering and scientific methods to oil drilling, assisting the burgeoning oil industry in establishing operating and safety standards.
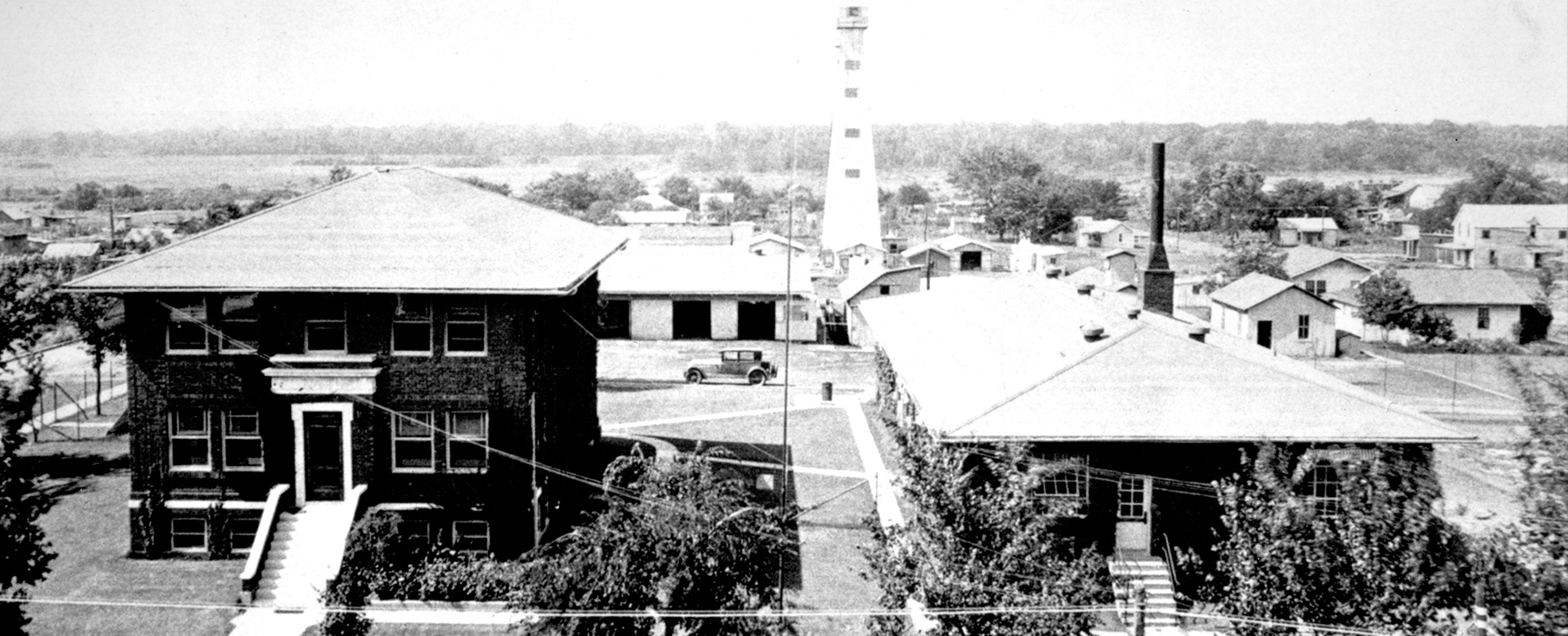
1919
The Bureau of Mines inaugurates the Pittsburgh Experiment Station in Pittsburgh’s Oakland section (now the site of Carnegie Mellon University’s Hamburg Hall). This station houses offices dedicated to mining, mine safety, explosives, metallurgy, fuels, and both chemical and electrical investigations.
1936
Following the Emergency Relief Appropriation Act of 1935, the Works Progress Administration expands research by constructing new station facilities. The Bartlesville Station transitions from a field demonstration center to a renowned research laboratory.
1946
National interest in synthetic fuels production intensifies post World War II, leading to the Synthetic Liquid Fuels Act of 1944. Consequently, the Synthesis Gas Branch Experiment Station is initiated at West Virginia University facilities in Morgantown, West Virginia. This 17-employee Station focuses on producing synthesis gas from coal.
1948
The Synthetic Liquid Fuels Act of 1944 promotes the establishment of energy research laboratories, resulting in the creation of the Bruceton Research Center near Pittsburgh, Pennsylvania.
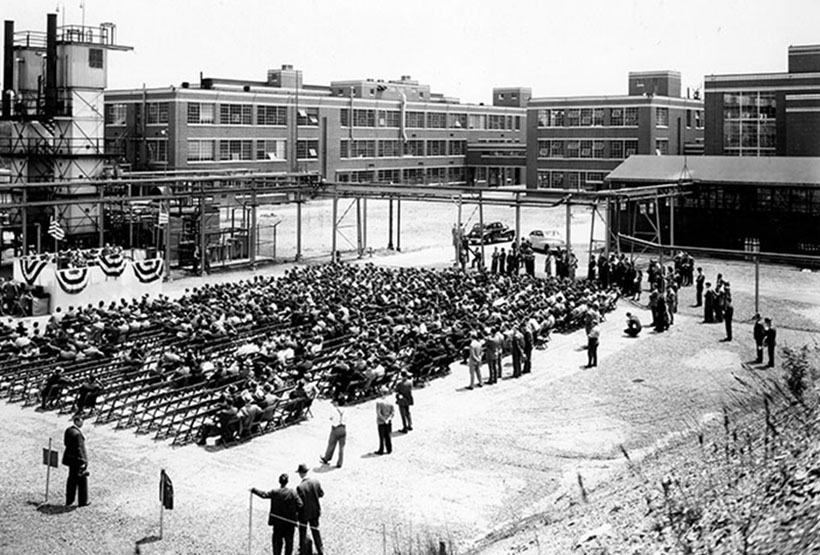
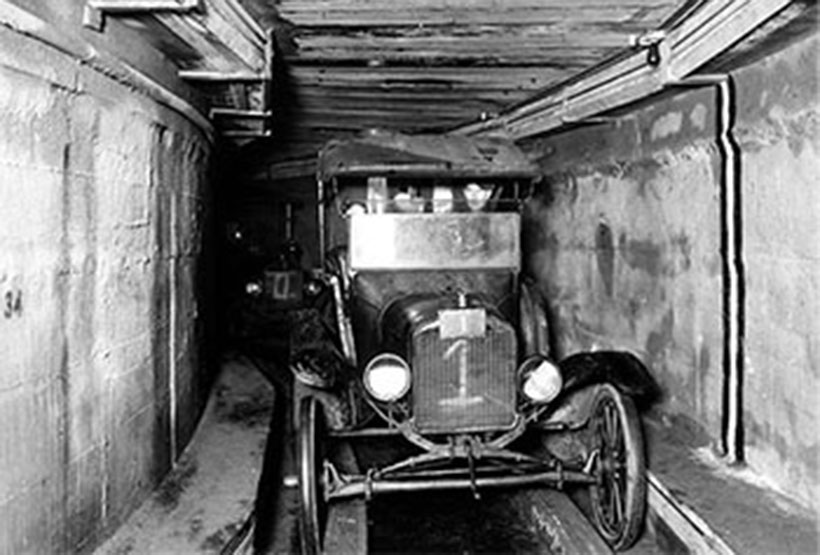
1954
The Appalachian Experiment Station begins operations in Morgantown, West Virginia, consolidating three distinct DOI groups.
1975
The U.S. Energy Research and Development Administration integrates the former DOI sites, and these centers begin overseeing federal contracts for fossil energy research and development.
1977
Under the U.S. Department of Energy (DOE), the three sites are rebranded. They now focus on research in coal, oil, and gas technologies and manage substantial contracts for research and development.
1983
The National Institute for Petroleum and Energy Research (NIPER) is established, and DOE creates the Bartlesville Project Office to supervise NIPER’s activities.
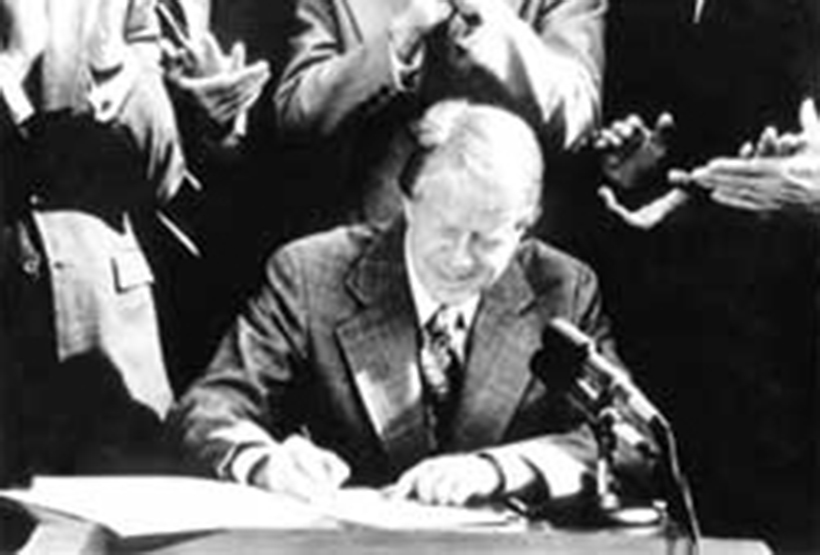
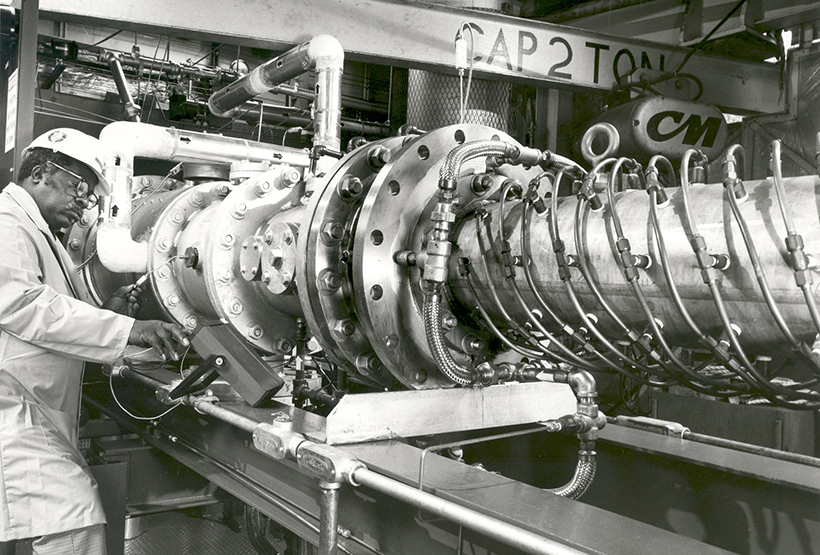
1993
DOE selects BDM-Oklahoma Inc. for the Bartlesville facility's operations and the University of Tulsa to spearhead a robust technology-transfer program.
1996
The Federal Energy Technology Center (FETC) emerges, combining METC (Morgantown) and PETC (Pittsburgh).
1998
To align with national energy goals, DOE launches the National Petroleum Technology Office (NPTO) in Tulsa, Oklahoma.
1999
The Secretary of Energy designates FETC as the National Energy Technology Laboratory (NETL).
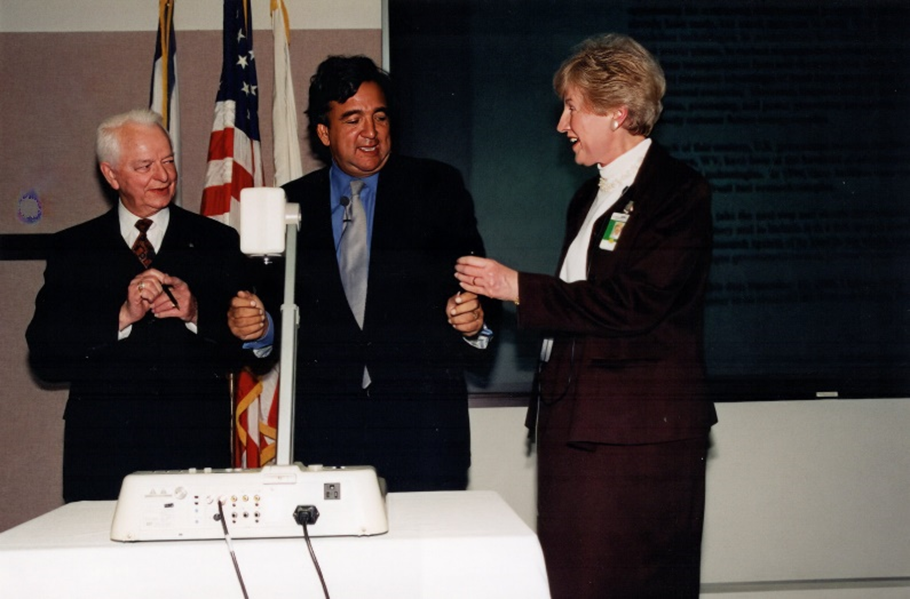
2000
NPTO becomes part of NETL, fostering collaboration and technology exchange among various sites.
2001
Following the NIPER site's transfer, DOE hands over the NIPER property to the City of Bartlesville. That same year, NETL opens the Alaska strategic office.
2005
The Albany Research Center (ARC) in Albany, Oregon, is brought under NETL management.
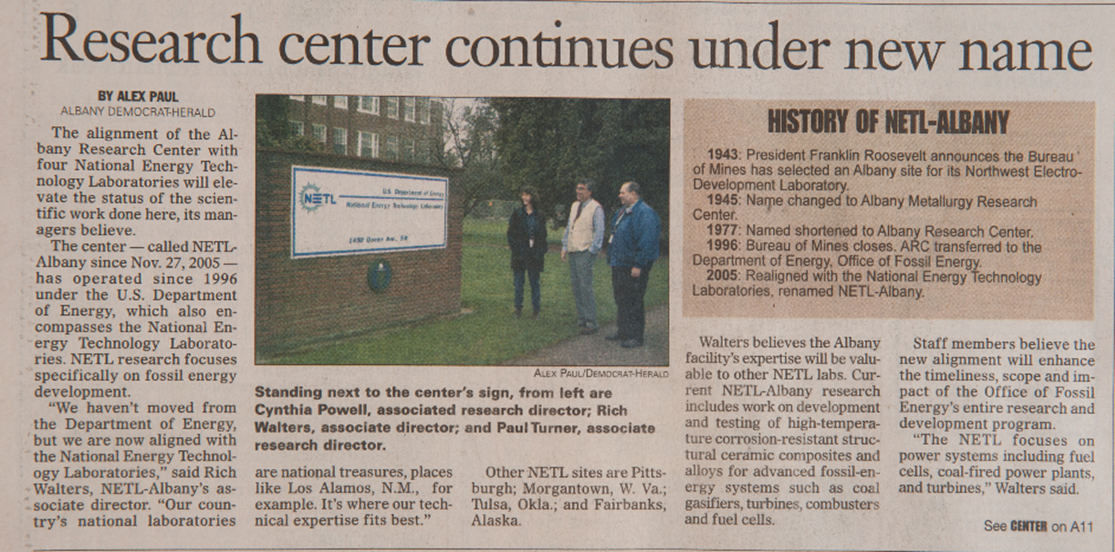
2009
NETL relocated its Oklahoma office to Sugar Land, Texas, positioning closer to the central hub of the American energy industry.
2019
To further strengthen ties with the world's top energy firms, NETL opened a strategic office in Houston, Texas.